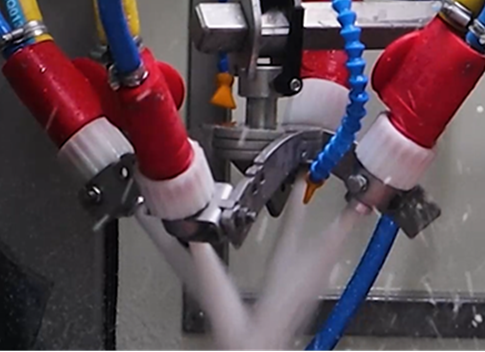
What is Wet blasting
Wet blasting, or vapor blasting as it is also know is a very versatile process that allows for true process control, meaning that we can achieve levels of consistency, accuracy and repeatability that other surface preparation and finishing methods cannot.
About Wet blasting?
Wet blasting is a surface finishing process that utilizes the flow of water-borne abrasive to achieve a desired finish on a component. The key advantage of wet blasting lies in the lubrication and flushing action of water during the blasting process. This results in a finer finish compared to dry grit and bead blasting methods.
In dry grit and bead blasting processes (illustrated in diagrams 1 and 2), the abrasive particles are propelled onto the surface without any water involvement. One notable issue with these dry methods is the severe 90-degree ricochet that occurs upon impact, which can lead to a less controlled and potentially damaging process.
On the other hand, wet blasting (depicted in diagram 3) introduces water into the blasting process. The water provides cushioning, and the altered angle of the media (abrasive particles) in combination with the water's flow produces a lapping effect. This lapping effect travels across the surface of the component being blasted, resulting in a satin/polished finish that is desired and preferred by many industries.
One significant advantage of wet blasting is its ability to eliminate unwanted media impregnation into components. This is in contrast to dry blasting methods, where residual media can become embedded in the blasted surface, potentially causing issues. As a result, wet blasting is considered a more modern and effective method for achieving the best surface finish in various applications.
The Wet blasting Process
Wet blasting, also known as vapor blasting, is a surface preparation or finishing process.
Wet blasting uses a mixture, which is made up of water and a media, (usually abrasive but not always) which we call the slurry. This mixture is propelled onto a surface using compressed air to clean, finish, or create a specific surface roughness, and can be used for a wide number of other applications. Although compressed air does propel the slurry at the surface, the method of processing is flow over the surface rather than pure impact. A by product of the process is washing meaning in many cases a pre-clean step is not necessary.
The process is inherently controllable when compared to other methods due to the carrier (water) and because of the constant monitoring and control on other process parameters.
Some of the other parameters used within our process are:
- Air pressure
- Air Volume
- Media concentration/density
- Water temperature
- Nozzle diameter
- Nozzle angle
- Component to Nozzle range
- Speed of process
- Automation if required
- Component Fixture
These parameters, along with other application specific parameters that we work with you on, work together to provide the highest level of process control, consistency and repeatability.
Wet blasting process benefits
Wet blasting offers several benefits for the automotive industry, making it a preferred method for various applications. We supply the global industry and have been doing so for over 30 years.
Here are some key advantages:
Highly controllable Surface Treatment: Wet blasting is a highly controllable process compared to other methods, such as dry blasting. It can effectively remove contaminants, coatings, burrs and rust without causing damage to delicate components, ensuring the integrity of the surfaces.
Washes & Degreases: The Wet blasting process uses water as a carrier and therefore a byproduct of the process is that it washed the components at the same time which means in many cases that a pre-clean step is not required.
No Dust Emission: The addition of water in wet blasting suppresses dust formation, resulting in a cleaner and safer working environment. This is crucial in the industries where cleanliness is essential for maintaining high-quality standards and ensuring the health and safety of workers. This also means no static build up or hazardous environments that can occur with some materials.
No static charge build up: Wet blasting does not create a static charge build up on components due to the water being used and therefore is a safer and also cleaner process. After processing your components will not be positively charged and therefor will not draw particles from the atmosphere toward them. This also removes the risk of an explosive atmosphere.
Environmentally Friendly: The use of water in wet blasting minimizes the environmental impact compared to dry blasting methods. It reduces airborne dust and facilitates easier containment and disposal of waste, contributing to environmental sustainability.
Can remove hazardous chemical processes: Wet blasting can remove the need for harsh and highly controlled caustic chemicals that are expensive to dispose of.
Versatility in Abrasive Media: Wet blasting can utilize a variety of abrasive media, such as glass beads, Aluminium oxide, Ceramics, or others, and due to the high level of control the process can also work wider a wider range of media sizes, from large coarse media to very fine if the requirement calls for it. This versatility allows manufacturers to choose the most suitable media for specific applications, providing flexibility in surface preparation.
Improved Surface Finish: Wet blasting not only cleans surfaces but also leaves them with a smoother finish. This is particularly beneficial for applications where a high-quality appearance is crucial, such as in the production of automotive parts with aesthetic requirements.
Minimized Heat Generation: Wet blasting generates less heat compared to some methods. This is advantageous for components that are sensitive to heat, preventing potential damage or distortion during the process.
Reduced Media Consumption: Wet blasting uses abrasive media more efficiently compared to other methods. The water cushions the impact and creates the ability to control and filter to a very fine level, allowing the media to be reused for a longer duration before replacement, and adds consistency and repeatability to process resulting in potential cost savings on other methods and a more accurate level of control over your process.
Enhanced Worker Safety: The reduction of dust and the generally lower abrasive impact contribute to a safer working environment for operators. Wet blasting helps mitigate health risks associated with exposure to airborne contaminants, improving overall workplace safety.