Medical Devices & Tooling Surface Treatment
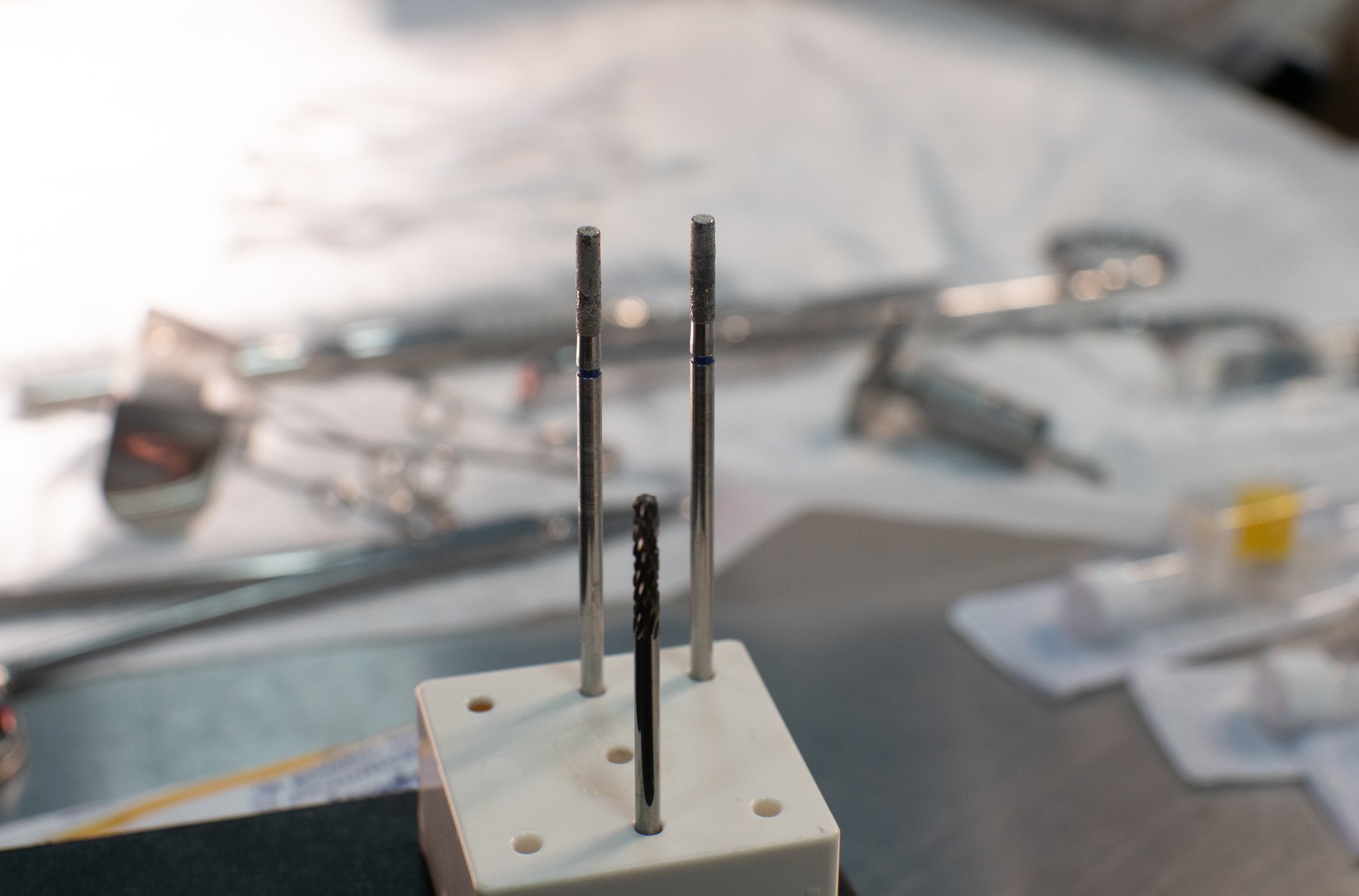
Consistency, accuracy and repeatability for medical device and tooling manufacture
Wet blasting finds various applications in the surface preparation and finishing of medical devices, and associated tooling. The process, which involves using a slurry of water, abrasive media, and sometimes additives, offers precision and control in achieving specific surface characteristics.
Benefits of Wet blasting for Medical devices & Tooling
Surface Cleaning and sterilisation: Removal of contaminants, residues, and impurities from the surfaces of medical devices and tooling. Ensures a clean and sterile surface for medical applications, reducing the risk of contamination.
Optimized Biocompatibility: Preparing surfaces to meet biocompatibility standards. Ensures that materials are safe for use within the human body.
Deburring and Edge Radiusing: Elimination of sharp edges, burrs, or irregularities from the edges of medical devices and tooling. Improves safety during handling and assembly, which is crucial in medical environments, where precision is paramount.
Rust and Corrosion Prevention: Removing existing rust or corrosion and preparing surfaces to resist future corrosion. Crucial for maintaining a sterile and corrosion-free state in medical devices and tools.
Surface Smoothing: Smoothing out rough surfaces on medical devices and tooling. Enhances hygiene, prevents areas for bacterial accumulation, and contributes to a smoother finish.
Selective Material Removal: Targeted material removal in specific areas without compromising overall structural integrity. Provides precision in manufacturing, allowing for intricate designs and features.
Surface Finishing: Achieving a controlled and uniform surface finish on medical devices and tooling. Enhances aesthetics, facilitates easy cleaning, and meets quality standards.
Preparation for Coating: Creating an optimal surface for coatings or treatments. Improves adhesion of coatings, enhances corrosion resistance, and ensures durability.
Uniform Surface Finish: Achieving a consistent and uniform surface finish across the entire medical device or tool. Contributes to the overall appearance and performance of the device or tool.
.
Surface Texturing: Controlled surface texturing for specific functionalities or aesthetic purposes. Customization of devices or tools for enhanced functionality or appearance.
These applications showcase the versatility of wet blasting in addressing various surface preparation and finishing needs in the medical device and tooling industry, contributing to the production of high-quality and reliable products.
Wet blast process Benefits
Our wet blasting process offers several inherent benefits that make it the preferred surface processing method for many industries and applications. Some of the key process benefits are listed below.
Highly controllable Surface Treatment: Wet blasting is a highly controllable process compared to other methods, such as dry blasting. It can effectively remove contaminants, coatings, burrs and rust without causing damage to delicate components, ensuring the integrity of the surfaces.
No Dust Emission: The addition of water in wet blasting suppresses dust formation, resulting in a cleaner and safer working environment. This is crucial in the industries where cleanliness is essential for maintaining high-quality standards and ensuring the health and safety of workers. This also means no static build up or hazardous environments that can occur with some materials.
Environmentally Friendly: The use of water in wet blasting minimizes the environmental impact compared to dry blasting methods. It reduces airborne dust and facilitates easier containment and disposal of waste, contributing to environmental sustainability.
Non-reflective finish: Wet blasting can achieve the surface roughness requirement needed with also the aesthetic appearance needed, such as a bright satin, as opposed to a reflective surface that can cause distraction within procedures.
Versatility in Abrasive Media: Wet blasting can utilize a variety of abrasive media, such as glass beads, aluminium oxide, Ceramics, or others, and due to the high level of control the process, can also work wider a wider range of media sizes, from large coarse media to very fine if the requirement calls for it. This versatility allows manufacturers to choose the most suitable media for specific applications, providing flexibility in surface preparation.
Improved Surface Finish: Wet blasting not only cleans surfaces but also leaves them with a smoother finish. This is particularly beneficial for applications where a high-quality appearance is crucial, such as in the production of automotive parts with aesthetic requirements.
Minimized Heat Generation: Wet blasting generates less heat compared to some methods. This is advantageous for components that are sensitive to heat, preventing potential damage or distortion during the process.
Reduced Media Consumption: Wet blasting uses abrasive media more efficiently compared to other methods. The water cushions the impact and creates the ability to control and filter to a very fine level, allowing the media to be reused for a longer duration before replacement and adds consistency and repeatability to process resulting in potential cost savings on other methods and a more accurate level of control over your process.
Enhanced Worker Safety: The reduction of dust and the generally lower abrasive impact contribute to a safer working environment for operators. Wet blasting helps mitigate health risks associated with exposure to airborne contaminants, improving overall workplace safety.
In summary, wet blasting provides a combination of precision, environmental responsibility, cost-effectiveness, and safety benefits, making it a superior method and attractive option for various industry applications
Process Driven Solutions for Medical devices & Tooling
Our aim is to work with you and supply you the process and solution(s) to meet your requirements.
Our equipment is designed to best utilise our process to meet your requirements. By utilising our years of experience and process knowledge, and combining it with our automated technology, we can provide a complete solution that delivers control and consistency to give you the perfect finish every time.
Contact us to discuss your requirements, and how we can work with you. Or have a look at our solution pages for more information.
We also design and manufacture washing equipment which in many cases complements our wet blasting solutions.
In many applications we have implemented solutions that incorporate both blasting and washing in a one step process which can remove handling steps and increase efficiency.
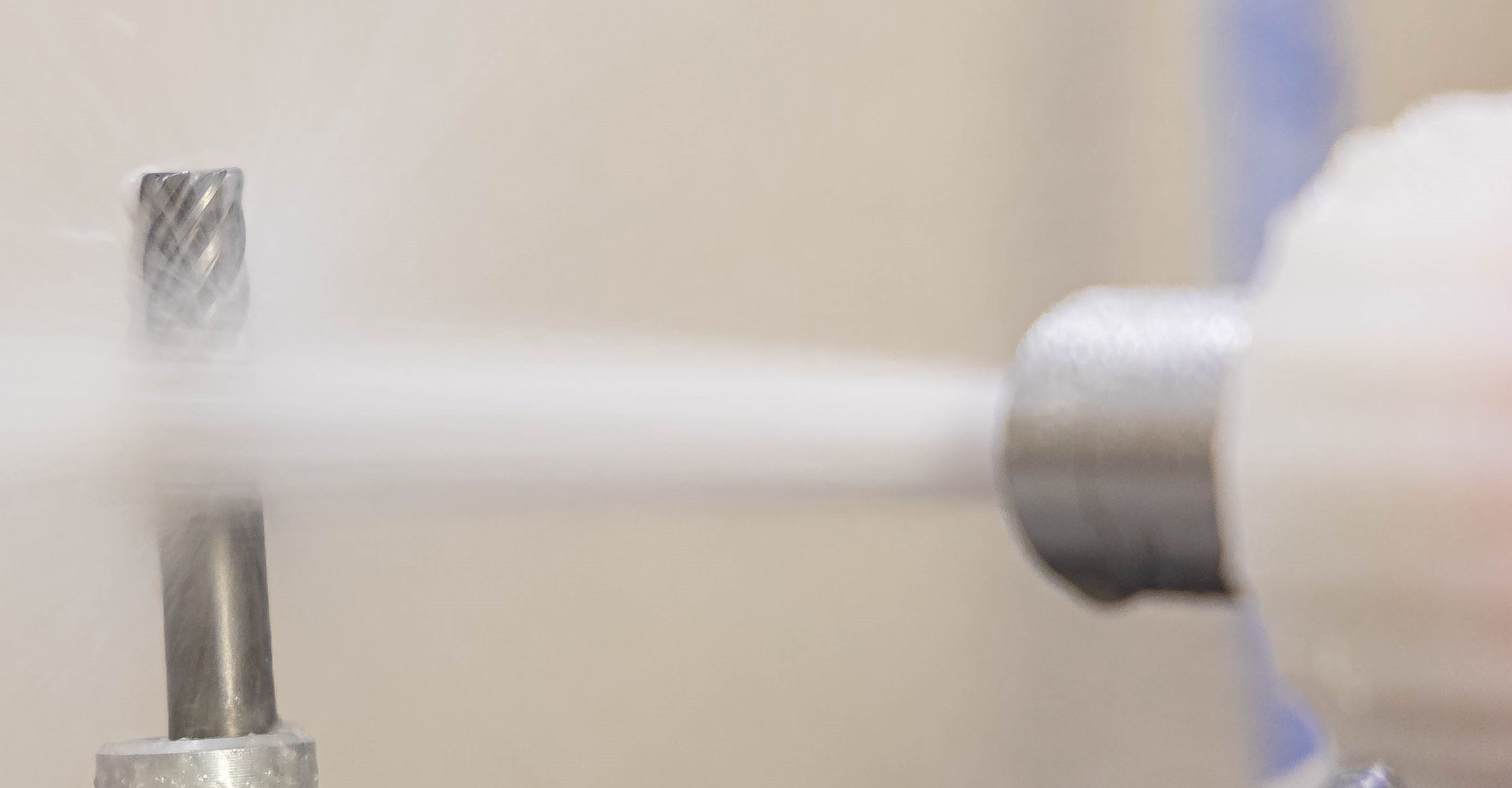