Wet Peening
Easy peening of components to increase longevity
Wet blast peening, also known as wet peening or wet abrasive peening, is a surface treatment process that combines the principles of wet blasting with shot peening.
This technique involves using a slurry of abrasive media mixed with water to impact the surface of a material, inducing compressive stresses and improving the material's fatigue strength. Wet blast peening is often employed for enhancing the performance and longevity of metal components.
Wet Blasting Applications for Wet Peening
Wet blast peening combines the benefits of shot peening and wet blasting. Shot peening involves the controlled bombardment of a material's surface with small, rounded particles (shot) to induce compressive stresses. Wet blasting introduces water into the process to reduce dust and control the temperature generated during impact. Some of the industries that utilise this are:
Aerospace: Wet blast peening is widely used in the aerospace sector for treating critical components, such as aircraft engine parts, turbine blades, landing gear components, and structural elements. The process helps improve fatigue resistance and prolong the lifespan of these high-stress components.
Automotive Components: Critical automotive components, including engine parts, transmission gears, and suspension components, can benefit from wet blast peening. The treatment enhances fatigue strength and resistance to wear, contributing to improved reliability and durability.
Power Generation: Components in power generation equipment, such as turbine blades, rotors, and generator shafts, are often subjected to cyclic loading. Wet blast peening helps extend the life of these components by improving their fatigue resistance.
Oil and Gas Industry: Wet blast peening is used in the oil and gas sector for treating components exposed to harsh environments. This includes components in drilling rigs, pipelines, and offshore platforms. The process enhances resistance to corrosion fatigue and stress corrosion cracking.
Tool and Die Manufacturing: Tools and dies used in manufacturing processes are subjected to wear and cyclic loading. Wet blast peening can be applied to increase the fatigue strength and durability of these critical components and or coatings.
Metal Springs: Springs used in various applications, such as automotive suspension systems or industrial machinery, can benefit from wet blast peening. The process helps increase their fatigue life and resistance to stress-induced failures.
Bandsaw Blades: Wet blast peening of bandsaw blades extends life and reduces failures due to fatigue and gullet cracks.
Wet blast peening is chosen for its ability to improve the mechanical properties of metal components while providing additional benefits such as surface cleaning and finishing. The applications are diverse, spanning industries where the reliability and longevity of metal components are critical considerations.
Wet blasting Benefits for Peening
Wet blasting can have several benefits when it comes preparing surfaces for coatings. Here are some advantages associated with using wet blasting for achieving specific surface finishes:
Surface Impact: The accelerated abrasive slurry impacts the surface of the material, causing plastic deformation and creating compressive stresses in the surface layer. The compressive stresses help improve the material's resistance to fatigue, cracking, and stress corrosion.
No Media Embedment: Wet blasting helps minimize abrasive embedment into the surface being treated. This is particularly beneficial for softer materials or sensitive substrates where avoiding damage or deformation is essential.
Surface Cleaning and Smoothing: Wet blasting not only removes contaminants and unwanted materials from surfaces but also helps in smoothing uneven surfaces. This can be advantageous when preparing surfaces for coatings, ensuring better adhesion and a more uniform finish.
Selective Material Removal: The wet blasting process allows for selective material removal, enabling operators to focus on specific areas or features while maintaining the overall surface integrity. This precision is crucial in applications where controlled material removal is required.
Heat Reduction: Wet blasting generates less heat compared to some dry blasting methods. This is important when dealing with heat-sensitive materials, as it helps prevent thermal damage while achieving the desired surface roughness.
No Dust: Wet blasting removes airborne dust, providing a cleaner and safer working environment. This is advantageous for both operator health and environmental considerations, especially in industrial settings where dust control is a concern.
Surface Finish: Wet blast peening not only induces compressive stresses but also imparts a surface finish to the treated material. The process can simultaneously clean and peen the surface, providing both functional and aesthetic benefits.
Environmental Considerations: Wet blasting is generally considered more environmentally friendly than dry blasting methods, as it reduces the release of abrasive dust and contaminants into the air. This is particularly important in areas where environmental regulations are stringent.
Process Driven Solutions for Wet Peening processes
Our aim is to work with you and supply you the process and solution(s) to meet your requirements.
Our equipment is designed to best utilise our process to meet your requirements. By utilising our years of experience and process knowledge, and combining it with our automated technology, we can provide a complete solution that delivers control and consistency to give you the perfect finish every time.
Contact us to discuss your requirements, and how we can work with you. Or have a look at our solution pages for more information.
We also design and manufacture washing equipment which in many cases complements our wet blasting solutions.
In many applications we have implemented solutions that incorporate both blasting and washing in a one step process which can remove handling steps and increase efficiency.
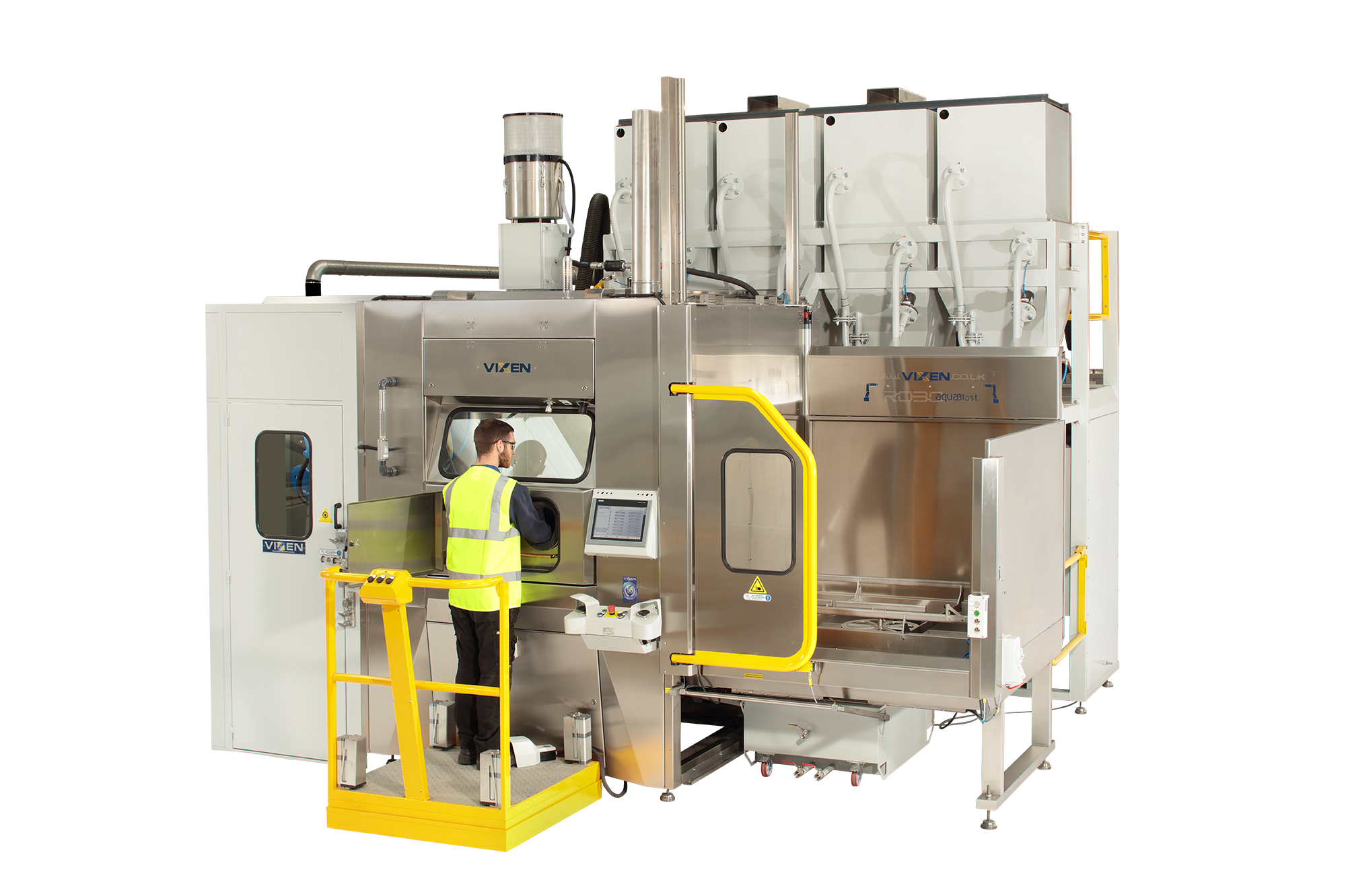