Wet Blasting Descaling
A cleaner, faster, and environmentally friendly process for descaling
Wet Blasting can be used for descaling, and is a surface preparation technique that uses a combination of water and an abrasive media, to remove scale, rust, oxides, and other contaminants from metal surfaces.
Descaling is a critical process in various industries, especially in metal fabrication and manufacturing, where the removal of surface impurities is essential for subsequent processes like coating, welding, or machining.
Wet Blasting Applications for Descaling
Wet blasting for the descaling of components and or surface finishing is used across a wide range of industries and can consolidate multi step processes in some cases.
With the wet blasting process, you will be descaling the surface, removing and scale build up and loose particles. The wet blast process works via flow rather than pure impact, utilising water, media, and compressed air to flow over the surface and scrub away any contaminants and scale.
Whilst many industries use our process for descaling some of the most common ones are:
Aerospace: Within the aerospace industry the descaling process can happen at OEM stage or MRO stage, depending on manufacturing method and material, where either oxidisation has happened through heat treatment and manufacturing or built up through life cycle use.
Our customers use their machines for removing scale from foundry cast parts, heat forming parts for the removal of scale and oxidisation through heat forming, and when overhauling an engine and components are going through NDT and need to be cleaned or 'descaled'.
Automotive: Descaling processes are important in the automotive industry to address issues such as rust, scale, and corrosion on various components. These processes are crucial for maintaining the performance, safety, and longevity of automotive parts.
There are many other industries, components and manufacturers that also need descaling as part of their manufacturing or remanufacturing process.
Each manufacturer will have individual requirements and understanding on process objectives. To see how we could work together on a process and solutions contact us to arrange sample processing on your components.
Benefits of Wet blast Descaling
Gentle on Surfaces: Wet blasting is less abrasive than dry blasting methods, making it suitable for delicate or sensitive materials.
Dust Suppression: The addition of water reduces dust, creating a safer and cleaner working environment.
Precise Control: Operators can control the pressure, water flow, and abrasive mixture, allowing for precise cleaning tailored to specific applications.
Environmentally Friendly: Wet blasting generates less airborne dust and is considered more environmentally friendly compared to some dry blasting methods.
Improved Surface Finish: Wet blasting can provide a smoother and more refined surface finish compared to traditional abrasive blasting methods.
Wet blasting is a versatile and effective method for surface preparation, offering a balance between the power of abrasive media and the precision needed for various applications.
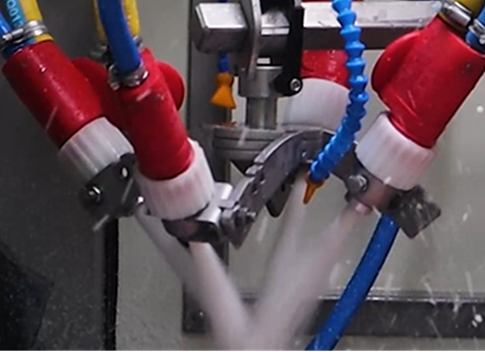
Process Driven Solutions for your Descaling Applications
Our aim is to work with you and supply you the process and solution(s) to meet your requirements.
Our equipment is designed to best utilise our process to meet your requirements. By utilising our years of experience and process knowledge, and combining it with our automated technology, we can provide a complete solution that delivers control and consistency to give you the perfect finish every time.
Contact us to discuss your requirements, and how we can work with you. Or have a look at our solution pages for more information.
We also design and manufacture washing equipment which in many cases complements our wet blasting solutions.
In many applications we have implemented solutions that incorporate both blasting and washing in a one step process which can remove handling steps and increase efficiency.