Wet Blasting Deburring
Fast, efficient, clean and targeted deburring
Wet Blasting is an effective method for deburring, especially when a more precise, and controlled approach are required, compared to traditional techniques. Wet blasting involves the use of a mixture of water, abrasive media to clean, deburr, and finish surfaces.
The process works via flow, not pure impact, which has the benefit of causing no damage to the surface, meaning potentially critical areas such as sealing faces are not altered, and will give a uniform and consistent finish. Wet blasting doesn’t require parts to be cleaned prior to processing, and can cope with oils. The process can utilise a wide array of media, allowing for individual requirements to be used depending on the material being processed.
Wet Blasting - Deburring Applications
Wet blasting for deburring is commonly used in industries such as aerospace, automotive, medical, and electronics, where precision and quality are critical. It offers an efficient and controlled method for removing burrs, while providing additional benefits such as dust suppression and improved surface finish.
Whilst many industries use our process, some of the most common industries using our wet blast technology for deburring are:
Aerospace: Deburring of aerospace components, such as turbine blades, engine components, and structural parts, where precision and material integrity are crucial. Wet blasting maintains the quality and dimensional accuracy of aerospace parts, ensuring they meet strict tolerances.
Automotive: Deburring of various automotive components, including engine parts, engine blocks, EV ECU machined parts, covers, transmission components, and chassis parts. Wet blasting provides a controlled and precise deburring process for automotive parts, contributing to the overall quality of the manufactured components, meaning critical areas such as sealing faces can be un-altered by the process.
Tooling: Deburring of cutting tools, dies, and molds used in machining and manufacturing processes. Wet blasting helps maintain the sharpness and longevity of cutting tools by removing burrs without compromising the tool's edge. This process can also remove other process steps and in some cases deburr and edge prep.
Precision Machining and Metal Fabrication: Deburring of precision machined parts and fabricated metal components. Wet blasting is effective for maintaining tight tolerances and achieving a smooth surface finish in precision machining and metal fabrication.
Optical Industry: Deburring of optical components, lenses, and delicate glass or plastic materials. Wet blasting ensures precise deburring without causing damage to sensitive optical surfaces.
Medical deburring: Deburring is a critical step in the manufacturing process of medical implants and devices. The precision and cleanliness required in the medical industry make deburring essential to ensure the safety and efficacy of these products. The dust free process of wet blasting is ideal for medical manufacturing cells.
There are many other industries, components and manufacturers that also need deburring as part of their manufacturing process.
Benefits of wet blast Deburring
Controlled Surface Treatment: Wet blasting is inherently more controllable than dry blasting, making it suitable for delicate or sensitive materials and accurate processes. It removes burrs without causing damage to the substrate. This also means on components with critical sealing faces these will be un-altered.
Dust Suppression: The addition of water in wet blasting helps suppress dust, creating a cleaner and safer working environment compared to dry blasting methods.
Precision Control: Control over variables such as water pressure, abrasive media, and nozzle distance among many others. This allows for tailored deburring according to specific requirements.
Reduced Heat Generation: Wet blasting generates less heat compared to other methods. This is beneficial for materials that may be sensitive to heat or for applications where heat generation is a concern.
Improved Surface Finish: Wet blasting can provide a smoother, and more refined surface finish compared to some dry blasting methods. This is particularly important when a high-quality surface finish is desired after deburring.
Selective Deburring: Wet blasting allows for selective deburring, making it possible to target specific areas of a workpiece without affecting other regions. This is advantageous for intricate or complex parts.
Cleaning and Degreasing: In addition to deburring, wet blasting can simultaneously clean and degrease surfaces. This makes it a versatile process for preparing components for further manufacturing or finishing.
Suitability for Various Materials: Wet blasting is suitable for a wide range of materials, including metals, plastics, and composites. It can be adapted to address the specific needs of different materials and applications.
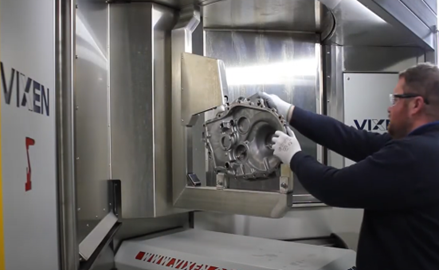
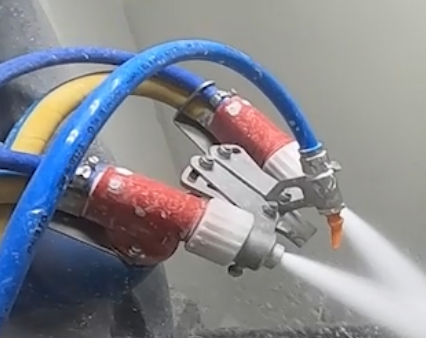
Process Driven Solutions for your Deburring Applications
Our aim is to work with you and supply you the process and solution(s) to meet your requirements.
Our equipment is designed to best utilise our process to meet your requirements. By utilising our years of experience and process knowledge, and combining it with our automated technology, we can provide a complete solution that delivers control and consistency to give you the perfect finish every time.
Contact us to discuss your requirements, and how we can work with you. Or have a look at our solution pages for more information.
We also design and manufacture washing equipment which in many cases complements our wet blasting solutions.
In many applications we have implemented solutions that incorporate both blasting and washing in a one step process which can remove handling steps and increase efficiency.