Improve Round Shank Tools with wet blasting
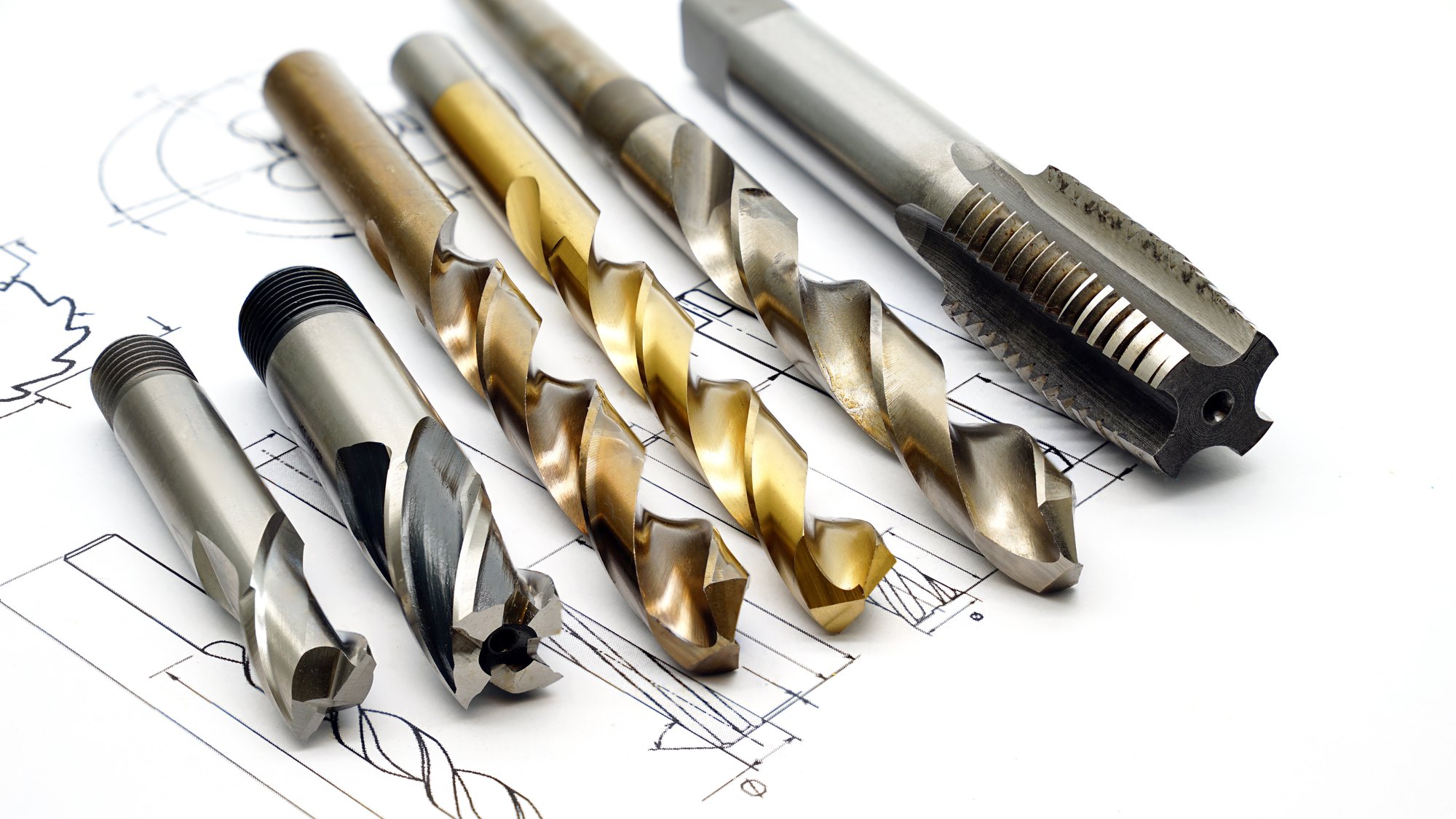
Increase Tool Value with Wet Blasting
Round shank tools are used in various applications, including machining, cutting, drilling, and milling. The choice of material for round shank tools depends on the specific requirements of the application, including the type of material being processed, the cutting conditions, and the desired tool properties.
Regardless of material, we see similar requests when discussing requirements with our customers. often, while moving through our samples processing and process development phases, we are able to show that our wet blasting process can achieve your specific tool needs.
Some of the materials that we work on with our customers for RST processing range from HSS, Tool Steel, Carbide and Diamond coated tools. These also range in size, and most commonly they is between 5mm to 25mm, but we also have requests for micro tool processing.
Benefits of Wet Blasting for RST finishing
Wet blasting offers several benefits for the manufacturing and finishing of RST making it an increasingly preferred method.
Here are some key advantages:
Highly controllable Surface Treatment: Our wet blasting process is highly controllable. Our solutions monitor and control many variables to ensure the consistent, and repeatable, processing of your tools
No Dust Emission: With the wet blasting process, no dust is created, and no static is built up. This not only creates a cleaner and safer environment, but also give the high levels of cleanliness needed in RST manufacture.
Environmentally Friendly: The use of water in wet blasting minimizes the environmental impact compared to other processing methods. It reduces airborne dust and facilitates easier containment and disposal of waste, contributing to environmental sustainability.
Versatility in Abrasive Media: Wet blasting can utilize a variety of abrasive media; due to the high level of control the process can also work wider a wider range of media sizes from large coarse media to very fine if the requirement calls for it. This versatility allows manufacturers to choose the most suitable media for specific applications, providing flexibility in surface preparation.
Minimized Heat Generation: Wet blasting generates less heat compared to some methods. This is advantageous for components that are sensitive to heat, preventing potential damage or distortion during the process.
Reduced Media Consumption: Wet blasting uses abrasive media more efficiently compared to other methods. The water cushions the impact, and creates the ability to control and filter to a very fine level, allowing the media to be reused for a longer duration before replacement. It also adds consistency and repeatability to process, resulting in potential cost savings on other methods, and a more accurate level of control over your process.
Enhanced Worker Safety: The reduction of dust and the generally lower abrasive impact contribute to a safer working environment for operators. Wet blasting helps mitigate health risks associated with exposure to airborne contaminants, improving overall workplace safety.
In summary, wet blasting provides a combination of high control and precision, environmental responsibility, cost-effectiveness, and safety benefits, making it a superior method and attractive option for your needs.
Wet Blasting Applications for RST
Wet blasting for RST is increasingly becoming the go to method for finishing tools, due to the process control and available results. Because our wet process can use such a wide range of media, and because of the high level of control, the process is able to achieve consistent and repeatable results. This allows for very fine accuracy and potential, combining the effects of multiple processes into one automated process step.
Many of the applications, if not all are linked to the desire to remove heat build, and enhance tool performance. This extends tool life along, with creating the perfect surface for adhesion and cutting geometry.
Some of applications our customers regularly use our wet blasting process for are:
Deburring: After machining or heat treatment the tools may have sharp edges or burrs. Wet blasting can be employed to remove these burrs and create a smooth, burr-free surface with minimal effect on the edge geometry. This will create the smooth finish desired and aid coating adhesion.
Pre coat Cleaning: Wet blasting is effective for removing contaminants, oils, and residues from the surfaces of round shank tools. This cleaning process is crucial to ensure optimal tool performance and coating adherence, Wet blasting can create a highly clean and reactive surface creating the ideal environment for the coating process.
Edge preparation and Honing: Wet blasting can be applied to provide a defined edge to the tools. The requirements of the edge size varies depending on customers requirements and end user application. By utilising our wet blast process, you can achieve consistent and repeatable results on your tools giving extended life of the tool and maximum coating adherence on the edge.
Surface Preparation: Before coating or heat treatment, round shank tools may require surface preparation to enhance adhesion and improve the quality of the finished product. Wet blasting provides a controlled method for achieving the desired surface roughness and cleanliness, creating an ideal substrate for subsequent treatments.
Post coat processing: Following the coating process and depending on the exact coating conditions and make up there are time that post coat processing can aid the tool performance by smoothing and or peening the surface for increased performance.
Each manufacturer will have individual requirements and understanding on process objectives. To see how we could work together on a process and solutions contact us to arrange Free sample processing on your tools.
Process Driven Solutions for your RST Manufacturing
Our aim is to work with you and supply you the process and solution(s) to meet your requirements.
Our equipment is designed to best utilise our process to meet your requirements. By utilising our years of experience and process knowledge, and combining it with our automated technology, we can provide a complete solution that delivers control and consistency to give you the perfect finish every time.
Contact us to discuss your requirements, and how we can work with you. Or have a look at our solution pages for more information.
We also design and manufacture washing equipment which in many cases complements our wet blasting solutions.
In many applications we have implemented solutions that incorporate both blasting and washing in a one step process which can remove handling steps and increase efficiency.