Fastener cleaning and finishing
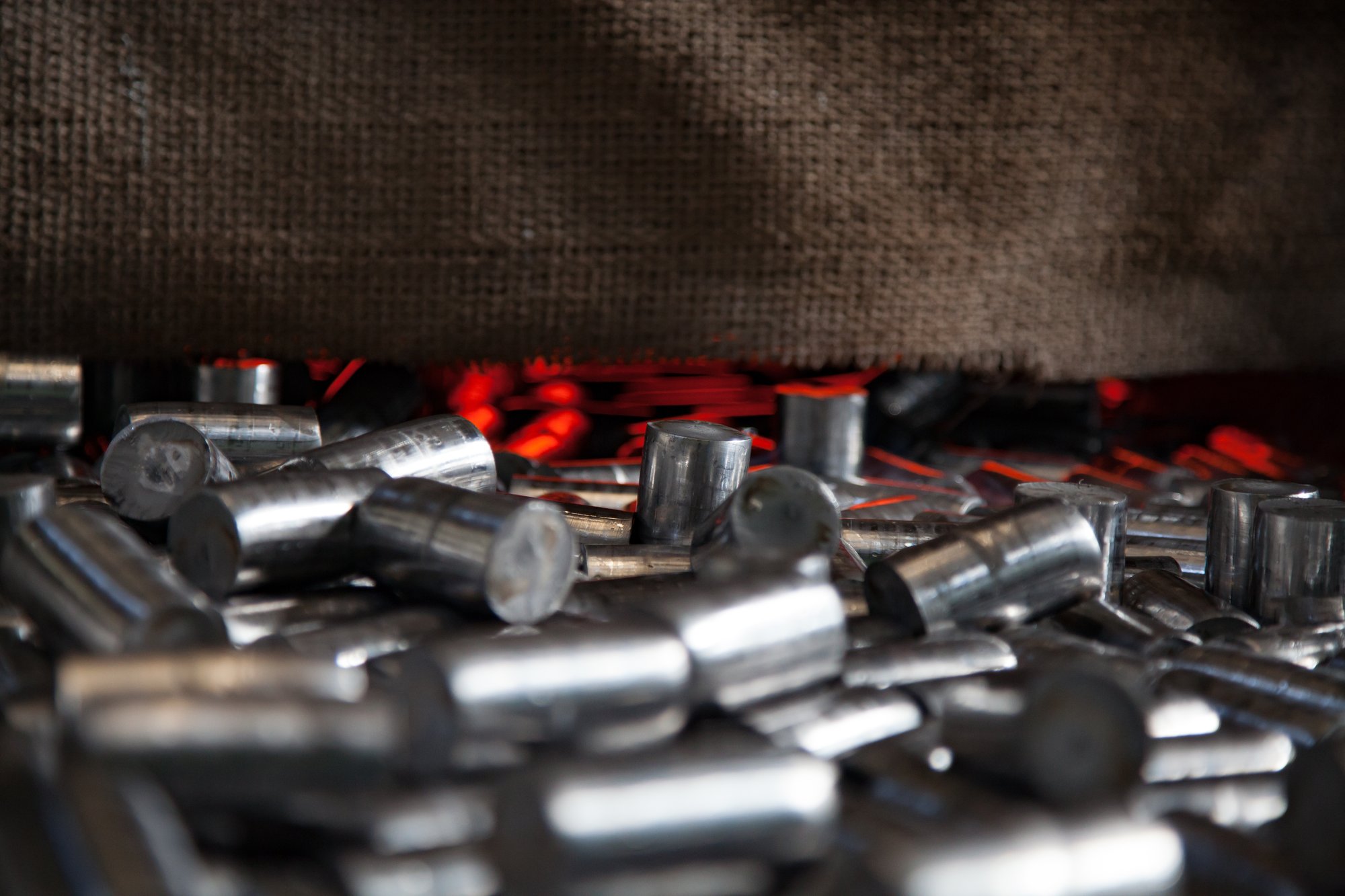
Automate blasting your batch, individual or complex fasteners including gears, rivets or spring finishing
Fastener surface finishing is a crucial aspect of the manufacturing process, influencing the performance, appearance, and longevity of fasteners. The choice of surface finishing method for fasteners depends on factors such as material type, intended application, environmental conditions, and aesthetic preferences. Manufacturers often employ a combination of techniques to achieve the desired properties for their fasteners.
Wet blasting (Also known as vapor blasting) is becoming a preferred method for fastener manufacturers because of the control, consistency, accuracy, and environmentally friendly process that wet blasting offers. Wet blasting also provides reduced processing steps, improved results, less touch points and working environment improvements, plus manufacturing flow and efficiency.
Benefits of wet blasting for fastener manufacture & finishing
Wet blasting offers several benefits for the manufacturing and finishing of fasteners making it an increasingly preferred method.
Here are some key advantages:
:Highly controllable Surface Treatment: Wet blasting is a highly controllable process compared to other methods such as dry blasting. It can effectively remove contaminants, coatings, burrs and rust without causing damage, ensuring the integrity of the surfaces.
No Dust Emission: The addition of water in wet blasting suppresses dust formation, resulting in a cleaner and safer working environment. This is crucial in industry where cleanliness is essential for maintaining high-quality standards and ensuring the health and safety of workers. This also means no static build up or hazardous environments that can occur with some materials.
Precision & Consistent Cleaning: Wet blasting allows for more precise control over the cleaning process. Operators can adjust variables such as water pressure, abrasive media, and nozzle distance, to name just a few, to achieve the desired level of cleaning without over-aggressive removal of material.
Effective Coating Removal: Wet blasting is highly effective in removing old coatings, paint, and other contaminants. This ensures the highest cleanliness levels and enhances adhesion and a durable finish.
Environmentally Friendly: The use of water in wet blasting minimizes the environmental impact compared to dry blasting methods. It reduces airborne dust and facilitates easier containment and disposal of waste, contributing to environmental sustainability.
Versatility in Abrasive Media: Wet blasting can utilize a variety of abrasive media, such as glass beads, Aluminium oxide, Ceramics, or others, and due to the high level of control, the process can also work wider a wider range of media sizes, from large coarse media to very fine if the requirement calls for it. This versatility allows manufacturers to choose the most suitable media for specific applications, providing flexibility in surface preparation.
Improved Surface Finish: Wet blasting not only cleans surfaces but also leaves them with a smoother finish. This is particularly beneficial for applications where a high-quality appearance or surface roughness is crucial.
Minimized Heat Generation: Wet blasting generates less heat compared to some methods. This is advantageous for components that are sensitive to heat, preventing potential damage or distortion during the process.
Reduced Media Consumption: Wet blasting uses abrasive media more efficiently compared to other methods. The water cushions the impact and creates the ability to control and filter to a very fine level, allowing the media to be reused for a longer duration before replacement. It also adds consistency and repeatability to process, resulting in potential cost savings on other methods and a more accurate level of control over your process.
Enhanced Worker Safety: The reduction of dust, and the generally lower abrasive impact, contribute to a safer working environment for operators. Wet blasting helps mitigate health risks associated with exposure to airborne contaminants, improving overall workplace safety.
Gentle Cleaning: Wet blasting is less aggressive than dry blasting methods, making it suitable for delicate or sensitive materials. Fasteners can be cleaned without the risk of damage or deformation.
Improved Surface Adhesion: Wet blasting can enhance surface adhesion by creating a profiled surface that promotes better coating adhesion. This is important when fasteners are subsequently coated with protective layers to prevent corrosion.
Environmental Considerations: Wet blasting is generally considered more environmentally friendly than dry blasting because it reduces airborne dust and contaminants. This can be particularly important in industrial settings where environmental regulations are stringent.
Aquablast Tumbler & Wash Line
Cleans, surface preps, washes and dries components
Process Video
360° 3D model video
Wet blast applications for fasteners
Our Wet blasting process and solutions are used across the fastener industry in many areas for the common reason that the process is consistent, controllable and an environmentally friendly alternative to other finishing techniques and can outperform other methods and save time.
Many of our solutions can Clean/Surface Prep - Wash - Rinse -Dry
Some of Applications we have worked on and continue to work on, range from:
Cleaning and surface coating removal: Wet blasting is effective for cleaning fasteners and removing forming oils and grease, rust, scale, or contaminants from the surfaces. This is particularly important for fasteners that may be going through a heat treatment and hardening process for which the parts must be contaminant free.
Deburring: Fasteners often have burrs or sharp edges left from manufacturing processes. Wet blasting can be used to deburr the edges of fasteners, ensuring that they are free from sharp protrusions.
Surface Preparation for Coating: Before applying coatings, such as paint or plating, fasteners may undergo wet blasting to achieve the desired surface roughness, cleanliness, and adhesion properties.
Selective Surface Modification: Wet blasting allows for selective surface modification, enabling targeted material removal, or the creation of specific surface textures on fasteners.
Removing Scale and Oxidation: Fasteners made of materials like steel may develop scale or oxidation over time. Wet blasting can efficiently remove these unwanted layers, restoring the appearance and performance of the fasteners.
Preventing Galling: For fasteners that may experience galling during use, wet blasting can be employed to create a smoother surface finish, reducing the likelihood of galling, and improving the fastener's performance.
Composite: Composite fasteners or fixings typically need a clean undamaged and reactive surface for the adhesives to be applied. Wet blasting achieves this without damaging the surface make up
Each manufacturer will have individual requirements and understanding on Their process objectives. To see how we could work together on a process and solutions contact us to arrange FREE sample processing on your components.
Process Driven Solutions for your fastener manufacturing
Our aim is to work with you and supply you the process and solution(s) to meet your requirements.
Our equipment is designed to best utilise our process to meet your requirements. By utilising our years of experience and process knowledge, and combining it with our automated technology, we can provide a complete solution that delivers control and consistency to give you the perfect finish every time.
Contact us to discuss your requirements, and how we can work with you. Or have a look at our solution pages for more information.
As you can see here with our blast and wash tumble line we also design and manufacture washing equipment which in many cases complements our Wet blasting solutions.
In many applications we have implemented solutions that incorporate both blasting and washing in a one step process where needed which can remove handling steps and add increase efficiency.
Contact us to discuss your automation requirements
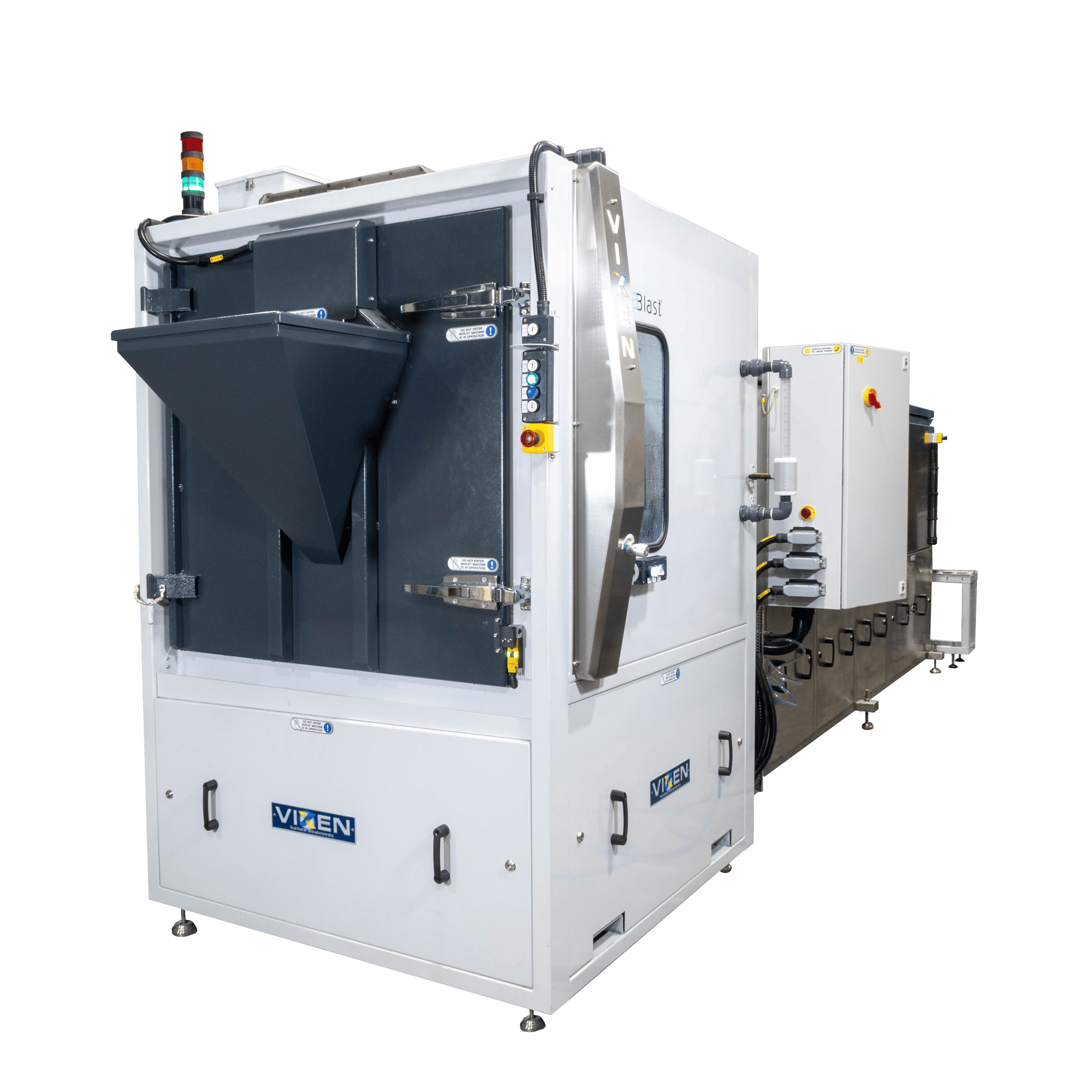