Aluminium Extrusion Die Cleaning
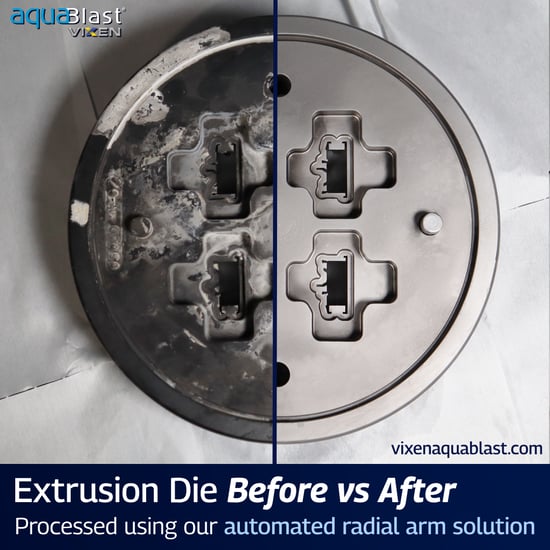
Industry-Leading Extrusion Die Cleaning Solutions
Extrusion dies operate in some of the most demanding industrial environments—facing extreme temperatures, high pressures, and the expectation of consistent performance over repeated cycles. To ensure longevity, efficiency, and reliability, proper and regular cleaning is essential. In particular, the bearing face surfaces must be maintained to the highest standard to maximize die life and protect the value they bring to your production process.
At Vixen Surface Treatments Ltd, our wet blasting (vapor blasting) technology has been engineered specifically to meet these challenges. Our solutions deliver a technical and economic edge—helping you extend die life, improve efficiency, reduce downtime, and ultimately lower your operational costs.
Benefits for extrusion die cleaning
Proven Wet Blasting Solutions for Extrusion Die Cleaning
Our wet blasting process—also known as vapor blasting—has been trusted by the global extrusion industry for decades. This advanced, flow-based cleaning method is ideally suited for precision die maintenance and offers a range of key benefits:
-
Reduced overall cleaning time and fewer die shop corrections
-
Flow-based cleaning action, not reliant on aggressive impact
-
Extended die life and value compared to traditional methods
-
No dimensional change to critical die features
-
Effective on complex geometries and internal features
-
Consistent and uniform finish on every cycle
-
Highly efficient compared to intensive manual labor methods
-
Streamlines die shop operations, improving productivity
Whether you’re cleaning extrusion dies made from tool steel, nitrided surfaces, or with intricate port shapes—our wet blast systems deliver unmatched precision and reliability.
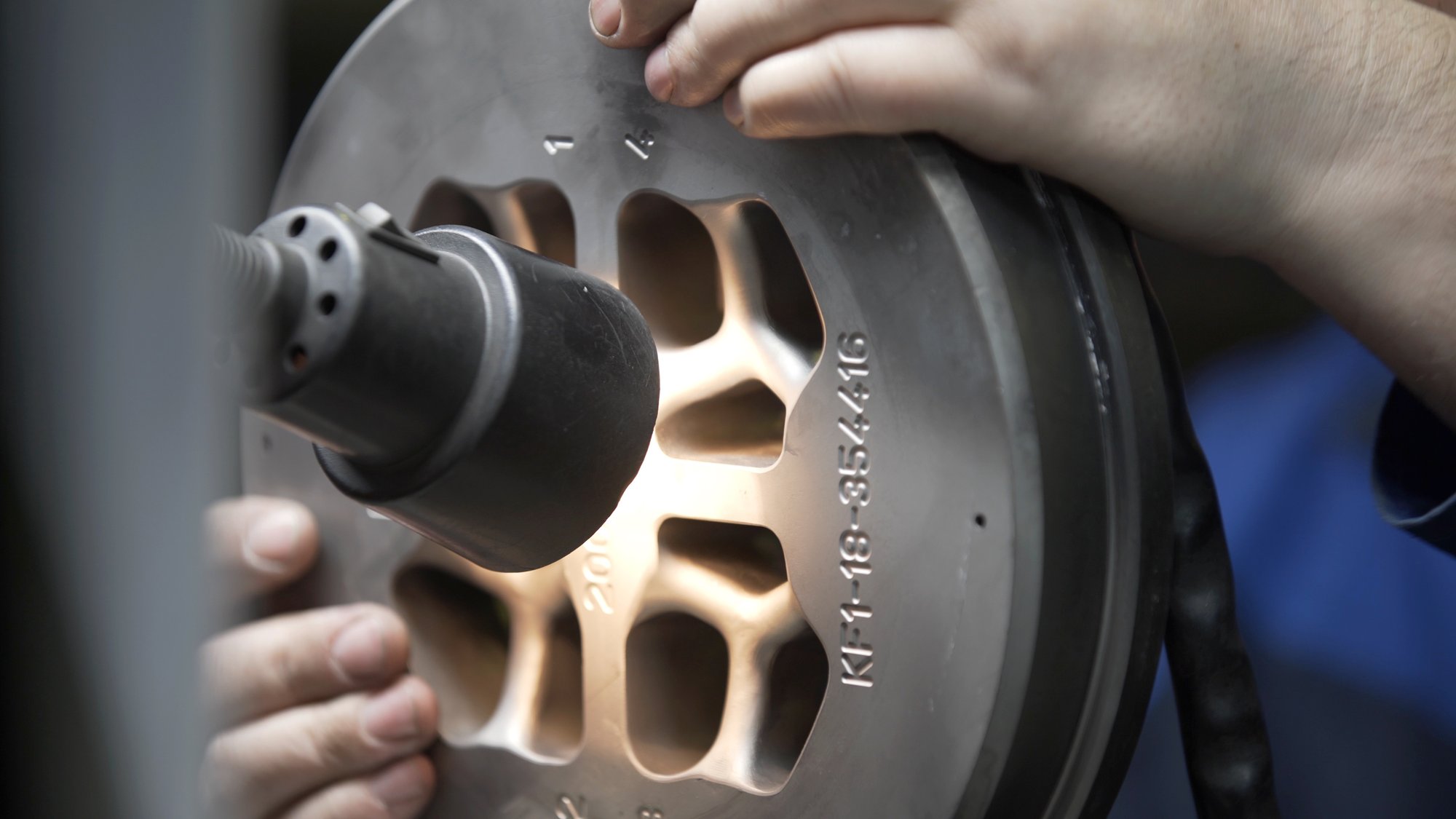
Process Driven Solutions for Extrusion Die Cleaning
Throughout the years of working with our customers and partners within this industry, we have developed our designs and process to provide you with the best solutions within the industry.
We have a standard offering of manual and fully automated solutions to fit the requirement of small to large capacity requirements. We can meet the needs of your specific production, and provide a solution to clean the dies that are integral to your business.
All our aluminium extrusion die solutions have features that allow you to make them bespoke to your individual needs.
Some of the options that may fit with your requirement are:
- External loading turntable to allow overhead crane loading or lifting
- Dual end or side loading. This feature allows for multiple tables meaning no lost time between cycles as one table can be loaded whilst the other is being processed inside the machine.
- Manual or automated blasting depending on requirement
- High weight capacity to allow multiple dies or large bespoke die processing
- Manual blasting option even on automatic solutions to allow flexibility of process for one off dies or any other work
- Bespoke component fixture design for you to fit your dies